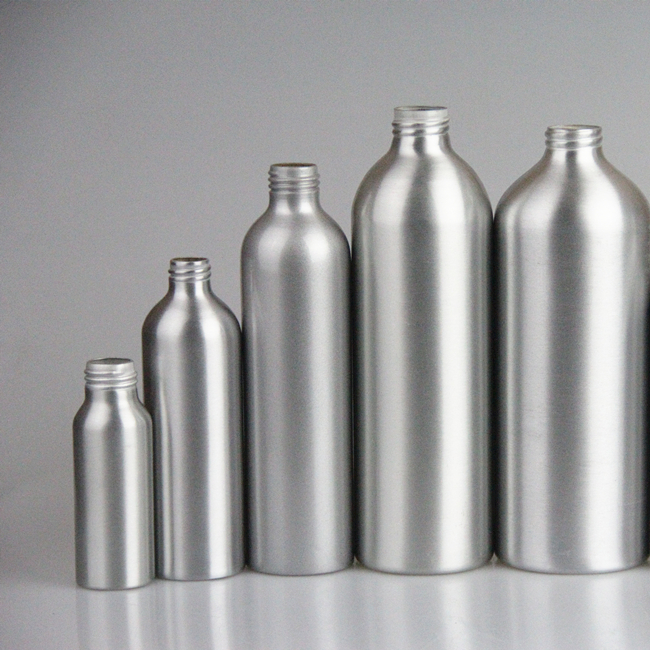
Do you ever think about how aluminum bottles remain strong and dependable?
Aluminum bottles have a special inner coatings, such as PPG coatings, to protect them from chemical changes. These coatings also increase their strength.
Picking the best coating goes beyond protection. It’s both scientific and practical. I remember discovering aluminum bottle coatings. It was like finding a hidden layer of safety for products. Every coating has a unique role and appeal. For example, I often choose coatings like PPG-3961 and PPG-2845. These coatings meet FDA rules and also consider environmental issues, such as BPA levels.
Exploring these choices might seem difficult. It’s about fitting the coating to your product’s requirements. Whether for lotion or drinks, the coating keeps your product fresh. Testing compatibility before big buys helps confirm everything is correct. It’s a really smart approach.
[claim claim=”PPG-3961 coating is BPA-free.” istrue=”false” explanation=”PPG-3961 contains BPA but is FDA-compliant.”]
[claim claim=”Aluminum bottles resist acids with specific coatings.” istrue=”true” explanation=”Coatings like PPG-3961 enhance resistance to acids and alkalis.”]
How Do Internal Coatings Protect Aluminum Bottles?
I recall the first time I asked myself why aluminum bottles resisted everything poured inside them. The secret reveals itself in their inner coatings!
Internal coatings in aluminum bottles act as hidden barriers. They stop chemical reactions between the aluminum and what is inside. This layer keeps products safe and strong. It really helps to keep everything pure and unchanged. Products stay fresh and very reliable.
The Science Behind Internal Coatings
Internal coatings fascinate me because they keep everyday things working well. These coatings act like strong armor for aluminum bottles1. They create a barrier that stops bad reactions between the metal and the contents. This barrier is especially important for acidic or alkaline products. Without it, bottles might look damaged.
Types of Coatings Used
Different coatings have appeared over time, each with unique qualities. For instance, PPG-3961 is a well-known example. It meets FDA standards and resists weak acids and alkalis, making it suitable for products like body lotions and hair sprays beautifully. In contrast, PPG-2845 is BPA-free, which is very important for those seeking non-toxic options.
Coating Type | Contains BPA | Uses |
---|---|---|
PPG-3961 | Yes | Body lotion, hair spray |
PPG-2845 | No | BPA-free applications |
Importance of Coating Selection
Selecting the correct coating feels like both science and art. It is about finding the right match between the coating and the product’s pH value and other chemical properties. Like a blind date between friends, compatibility matters. A poor match leads to unexpected problems, much like a bad dinner chat!
Color Variations in Coatings
Coatings have many colors – transparent, gold, beige, and more. The most used are gold and transparent coatings, but the best choice depends on what looks best for the product’s packaging2.
Safety and Testing Protocols
Testing is critical—not an afterthought. It resembles checking a parachute before a jump; it’s absolutely necessary! Regardless of the coating type, initial compatibility testing ensures no adverse reactions occur between the product and the coating. Conducting these tests helps prevent issues like leakage.
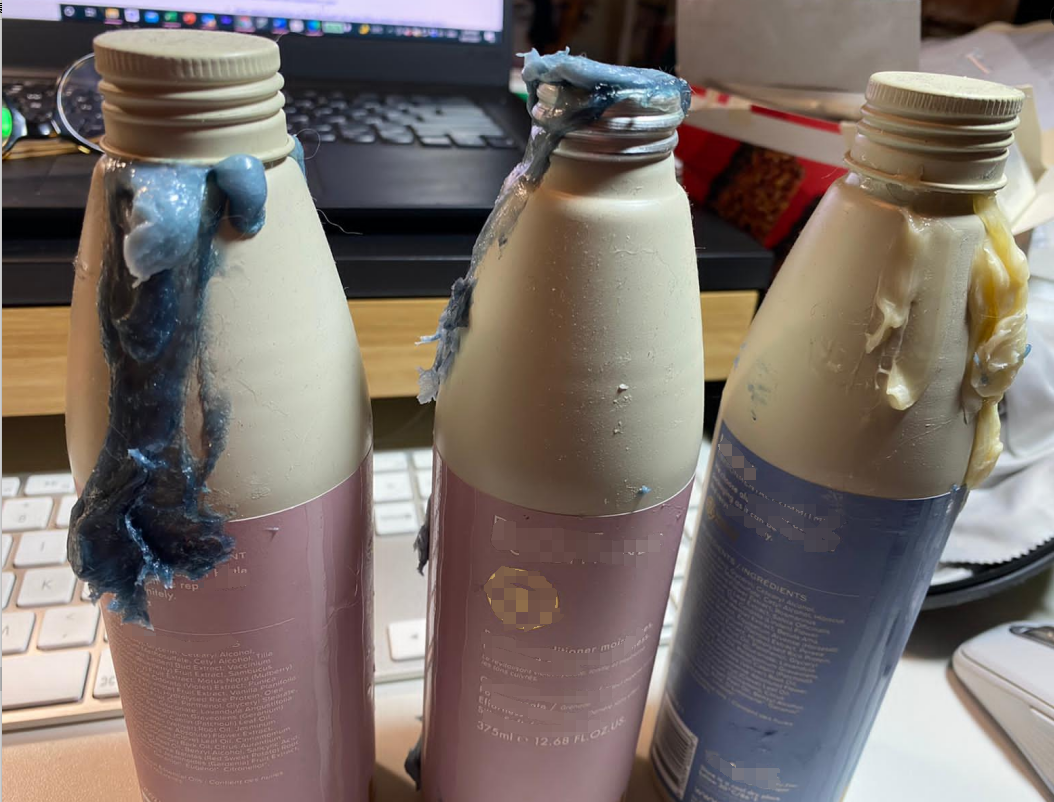
Knowing these details about internal coatings is really crucial for making packaging choices. They keep aluminum bottles3 reliable, ensuring contents stay safe and protected.
[claim claim=”Coatings prevent aluminum corrosion.” istrue=”true” explanation=”Internal coatings act as barriers to stop chemical reactions and corrosion.”]
What are the differences between PPG coatings?
When I first stepped into aluminum bottle packaging, the details of PPG coatings seemed very confusing. Learning about them was really important for keeping my products safe and high quality. Safety and quality mattered a lot.
PPG coatings differ mainly in their chemical makeup, resistance abilities and color choices. These coatings serve specific needs. Some types are safe for food. Others resist acid.
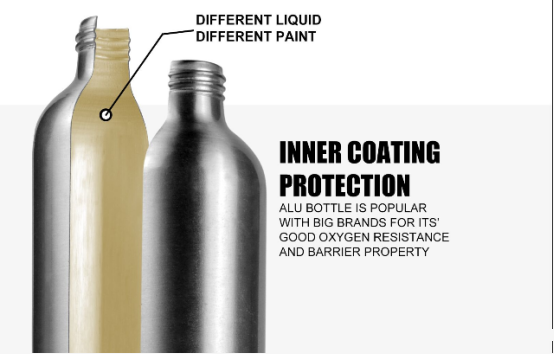
Chemical Composition and Food Safety
I remember when I first had to pick a coating for my items. The choice felt difficult, especially with food safety in mind. PPG-3961 includes bisphenol A (BPA) and meets FDA rules for food use. For people like me who care about health safety, PPG-2845 offers an option without BPA. This is important.
Coating Type | BPA Content | Food Grade |
---|---|---|
PPG-3961 | Yes | Yes |
PPG-2845 | No | Yes |
Resistance Properties
Different PPG coatings have special resistance features. These are important based on your item. For example, PPG-39614 handles weak acids and alkali, making it useful for things like body lotions and shower gels. This flexibility is something I found very helpful for my products.
Understanding these features helps avoid bad chemical reactions5 between the coating, container, and what’s inside.
Application-Specific Selection
Picking the right PPG coating isn’t only about appearance or safety. It’s about considering the product’s pH level6 and chemical mix. I learned early that testing for compatibility was crucial.
This check saved me from expensive errors and kept my brand’s reputation solid. Testing is critical.
Anyone using aluminum packaging for the first time should really focus on testing. It’s very vital to prevent issues like leaks or chemical problems that may harm product quality.
Choosing the right PPG coating isn’t just technical; it’s a promise to provide customers with quality and dependability.
Why Is Compatibility Testing Crucial for Aluminum Bottles?
Ever wondered why some aluminum bottles work perfectly while others fail? Understanding compatibility testing is key. It protects your product from unexpected issues. Compatibility testing is crucial.
Compatibility testing holds great importance for aluminum bottles. It stops chemical reactions that might happen between the bottle’s inside layer and what it holds. Testing guarantees product safety. Quality and rules need to be met.
Understanding Compatibility Testing
When I first entered the packaging field, compatibility testing seemed strange to me. Soon, I realized why it was so important. Compatibility testing checks the interaction between aluminum bottles and their contents. This helps confirm that the bottle’s inner coating does not react badly with what’s inside. Some popular options, like PPG-28457 and PPG-39618 coatings, meet FDA rules well.
Coating Type | BPA-Free | Common Applications |
---|---|---|
PPG-3961 | No | Body lotion, hair spray |
PPG-2845 | Yes | Food-grade products |
The Role of Internal Coatings
A colleague once shared a story about some aluminum bottles that failed terribly because they skipped testing the coatings properly. The coating inside aluminum bottles serves as a barrier. It protects against chemical reactions that can ruin the bottle. Testing is essential. The coating shields the material from corrosion and leakage. Newcomers in aluminum packaging should always check compatibility to avoid such disaster.
Preventing Chemical Reactions
Here’s a little tip: not every product suits every coating. Weak acids or bases might clash with certain coatings. For this reason, choosing a suitable coating for your product’s pH level is very important. It’s like dressing for the weather – choosing wrong might lead to discomfort or problems. Picking the right coating matters.
Certain products may react with elements in the coating. For example, weak acids or alkalis might interact with specific coatings9. Thus, selecting the right coating based on the product’s pH value is vital.
Regulatory Compliance and Safety
Early in my career, I learned why meeting regulatory standards was so vital through compatibility testing. This practice protects your brand from legal troubles and matches food safety standards. The FDA demands this for customer safety; it’s very important.
Conducting thorough compatibility testing aligns with regulatory standards, protecting your brand from legal issues. Compliance with food safety regulations, such as those set by the FDA, is crucial for consumer safety10.
Overall, knowing how coatings and product interactions happen can stop unwanted reactions, guarding safety and quality. Be it a BPA-Free option or a budget-friendly choice, always focus on compatibility testing before mass production; it surely provides peace of mind.
[claim claim=”PPG-3961 is BPA-free and used for food-grade products.” istrue=”false” explanation=”PPG-3961 is not BPA-free and is used for body lotion, hair spray.”]
[claim claim=”Weak acids can react with certain bottle coatings.” istrue=”true” explanation=”Weak acids may interact with specific coatings, affecting compatibility.”]
How do I choose the right coating for my product?
Exploring the world of coatings might seem like solving a puzzle with pieces like durability, safety and cost. These pieces fit together to shield your product.
Selecting the best coating for a product requires knowledge of its chemical compatibility, intended purpose and environmental factors. PPG coatings work well for food-related uses. However, testing for compatibility remains essential before starting large-scale production.
Understanding Coating Types
When I first explored different coatings, I saw how each type offers something special. Some types resist chemicals, and others protect from the environment. Look at PPG coatings11. They are very popular in packaging because they are safe for food and last a long time. Knowing this helped me understand coatings as more than just protection but as an important part of the product.
Testing and Validation
Testing is basically my rule. Before deciding on any coating, I do detailed compatibility tests. This step has saved me from problems like leaks or unwanted chemical reactions many times.
Cost vs. Performance
Balancing cost and performance feels like a tightrope walk. I often have to choose between safe coatings that are expensive and cheaper ones. It’s about finding that right balance for the product.
Leveraging Manufacturer Expertise
Talking to manufacturers feels like having a secret tool. Their knowledge about new coatings12 and trends has helped me find the best coating solution for my needs.
Considering these aspects has allowed me to choose coatings that not only protect but also maintain the quality of my products, really ensuring satisfaction throughout the process.
[claim claim=”PPG coatings are used in the packaging industry.” istrue=”true” explanation=”PPG coatings are popular for their food-grade compliance and durability.”]
[claim claim=”All coatings contain bisphenol A, affecting safety.” istrue=”false” explanation=”Not all coatings contain BPA; some are specifically BPA-free for safety.”]
Conclusion
Aluminum bottles utilize specialized coatings like PPG-3961 and PPG-2845 to enhance strength, prevent chemical reactions, and ensure product safety.
-
Learn about the science behind internal coatings and their protective properties to understand why they are essential for product safety. ↩
-
Discover how different colors in coatings can impact product presentation and meet specific aesthetic requirements. ↩
-
Explore why compatibility testing is critical to ensuring that aluminum bottles maintain their quality without leaks or corrosion. ↩
-
Learn about how different PPG coatings resist chemical reactions to protect your product. ↩
-
Discover why PPG-2845’s BPA-free property is beneficial for health-conscious consumers. ↩
-
Find out how pH levels can influence the effectiveness of various coatings. ↩
-
Learn about the types of PPG coatings used in aluminum bottles and their specific applications. ↩
-
Learn about the types of PPG coatings used in aluminum bottles and their specific applications. ↩
-
Understand how weak acids can interact with coatings in aluminum bottles, potentially leading to damage. ↩
-
Explore FDA regulations regarding aluminum bottle coatings to ensure compliance and safety. ↩
-
Explore this link to understand various industrial coatings and their specific uses, helping you choose the right option for your product. ↩
-
Discover methods for testing product compatibility with coatings to avoid potential risks and ensure quality. ↩