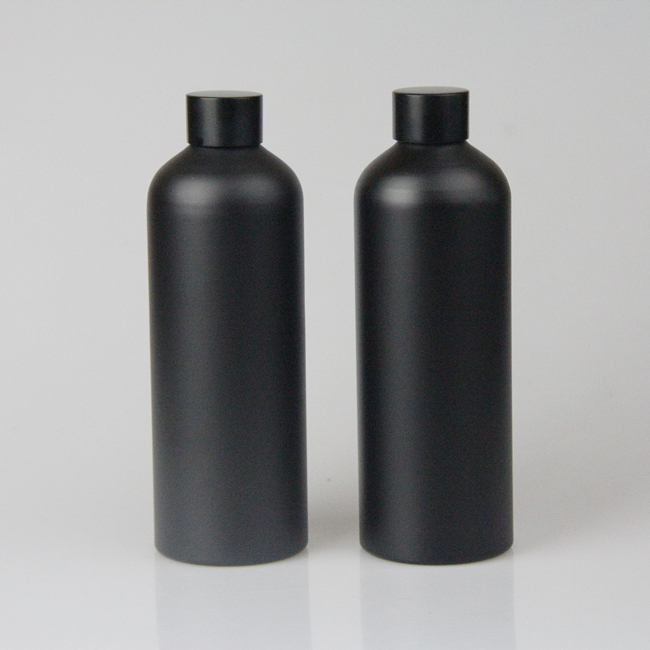
Are you thinking about aluminum bottles for your products? Trust me, this choice is worth exploring!
For 16 oz aluminum bottle packaging, knowing the benefits and uses is important. These bottles last a long time. They are good for the environment. Their design meets the needs of different industries. The design is also customizable.
As a CEO, I know the importance of picking the right packaging for our products. When I started using aluminum bottles, their modern look and eco-friendly nature impressed me. I recall seeing my brand’s logo printed on a 16 oz bottle. It was a real game changer! In this post, I share insights on custom logo printing. Inner coatings, sealing types and specific applications really improve your packaging.
[claim claim=”16 oz aluminum bottles are highly durable and sustainable.” istrue=”true” explanation=”Aluminum bottles provide excellent durability and are recyclable, making them a sustainable packaging option.”]
[claim claim=”Customization options for aluminum bottles are limited.” istrue=”false” explanation=”In reality, aluminum bottles can be extensively customized in design and features to meet diverse industry needs.”]
What makes aluminum bottles the best choice for packaging?
Have you ever thought about why aluminum bottles are now popular with many brands? These bottles have special benefits. They are different from typical packaging materials such as plastic or glass.
Aluminum bottles offer many advantages. Unique designs on bottles really help brands stand out. Protective coatings inside the bottles keep the product safe and fresh. Secure seals stop leaks effectively. Industries use these bottles in various ways. Aluminum bottles represent a truly sustainable choice. They improve product quality significantly while reducing harm to the environment.

Choosing the right packaging is very important for my products. As the CEO of a laundry detergent brand, this has been my focus. I remember when I first changed to aluminum bottles. It felt like a big step for my brand image and my environmental values. Let me explain some of the advantages that convinced me to take that step.
Custom Logo Printing
One of the standout features of aluminum bottles is the ability to personalize them through custom logo printing. This is not only about looks; it is about forming a bond with my customers. A vibrant, well-designed bottle attracts attention on a crowded shelf. Once I released my new aluminum bottles, I saw more customer loyalty. They probably felt closer to the brand and saw our values in our packaging.
Inner Coating
Aluminum bottles often come with special inner coatings that protect product integrity. This was very important because I wanted my detergent to stay fresh and effective. Different coatings serve different purposes, including:
Coating Type | Purpose |
---|---|
Epoxy | Provides a barrier against chemicals |
Polyethylene | Ideal for beverages, prevents flavor transfer |
UV Protective Coating | Shields sensitive products from light |
Using the correct inner coating kept my products uncontaminated and maintained their quality. I felt reassured knowing I was giving the best to my customers.
Sealing Types
Aluminum bottles offer several sealing options for safety and longevity. I struggled with leakage in my old packaging, which could have harmed my brand’s reputation. Luckily, aluminum bottles have great solutions:
- Screw Caps: Secure seal and easy to open.
- Child-Resistant Caps: Important for safety-focused customers.
- Tamper-Evident Seals: They confirm product safety for buyers.
Each seal fits specific needs, preventing leaks and keeping freshness, which I truly appreciate.
Applications
Aluminum bottles are very versatile and suit many industries. For me, they work well in:
- Personal Care: I thought about using them for shampoos and conditioners.
- Beverages: Perfect for water and juices – imagine the opportunities!
- Pharmaceuticals: Lightweight and protective – great for liquid medicines.
These possibilities confirmed my decision to use aluminum bottles as they fit my packaging strategy and match perfectly with my sustainability commitment. If you want more information on sustainable packaging options, check out this resource1.
[claim claim=”Aluminum bottles can be customized with logos for branding.” istrue=”true” explanation=”Custom logo printing on aluminum bottles enhances brand visibility and fosters customer loyalty through personalized designs.”]
[claim claim=”Aluminum bottles are unsuitable for beverages due to chemical reactions.” istrue=”false” explanation=”With specialized inner coatings, aluminum bottles are safe for beverages, preventing chemical reactions and maintaining product integrity.”]
How does custom logo printing enhance branding on aluminum bottles?
Do you ever think about how a simple logo on a metal bottle changes a brand’s identity? Custom logo printing is very important. It increases brand visibility and builds a strong link with customers.
Custom logo printing increases branding on aluminum bottles by adding visibility. It strengthens brand identity and creates a memorable experience for customers. This approach is very important for businesses that want to stand out in crowded markets.
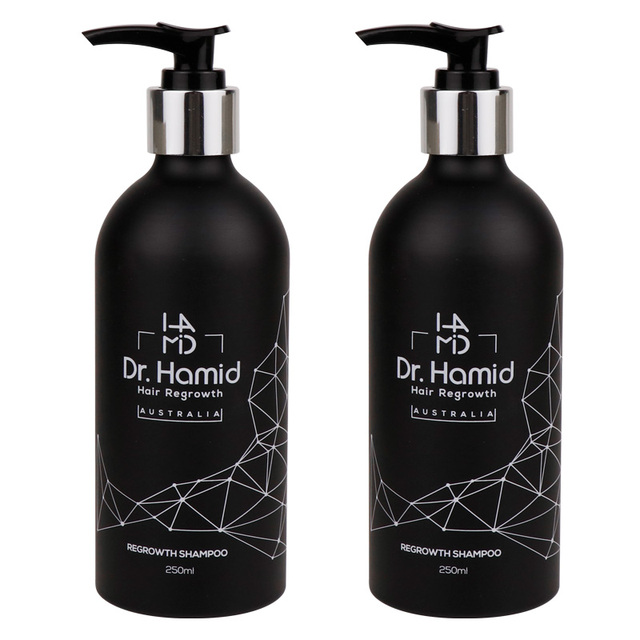
The Importance of Custom Logo Printing
Custom logo printing on aluminum bottles has a lot of power. I remember my first time seeing the impact of branding. I had just entered the product development field and felt amazed at how a logo could draw in customers. Logos are not only about looks but telling stories. A strong logo shows people who you are and what you believe in.
For example, if Matt’s laundry detergent brand uses vibrant colors and a distinctive logo, consumers will easily associate the product with its commitment to quality and environmental sustainability. This can lead to increased customer loyalty and engagement. By choosing aluminum bottles, the branding becomes even more impactful due to the sleek and modern appearance of the packaging.
Techniques of Custom Logo Printing
I learned many custom printing techniques for aluminum bottles:
- Screen Printing: Offers vibrant colors and lasts long. It is ideal for bold statements.
- Digital Printing: Great for detailed designs and small batches. It allows creativity without limits.
- Heat transfer Printing: Excellent for complex designs.This method creates detailed, multi-color patterns that are both vibrant and durable, making it ideal for intricate artwork on surfaces like fabric or aluminum.
Choosing the right technique may seem difficult, but it’s about matching your brand’s needs with what’s possible. For instance, Matt chose digital printing for a fast, small batch. It was perfect and spotless!
Inner Coating Benefits
Inner coatings in aluminum bottles are important. They do more than just protect what’s inside; they build a complete brand experience. Imagine a branded bottle that keeps your drink fresh!
I launched eco-friendly drinks and focused on our inner coating. It matched our brand perfectly. This detail caught eyes and confirmed the product’s quality. These small things turn regular products into unforgettable ones.
Applications of Custom Aluminum Bottles
Custom logos on aluminum bottles have wide uses:
- Personal Care Products: Eco-friendly packaging draws in aware consumers; it builds brand loyalty.
- Beverages: A drink with a custom brand stands out, creating excitement at events!
- Pharmaceuticals: Clear branding in crowded markets earns recognition and trust.
By strategically applying custom branding in these areas, businesses like Matt’s can significantly enhance their market presence and connect deeply with customers. Using aluminum bottles with custom logos is practical; more importantly, it’s about forming a strong brand identity that emotionally connects with consumers.
[claim claim=”Custom logos on aluminum bottles boost brand visibility.” istrue=”true” explanation=”Displaying custom logos prominently enhances brand recognition and visibility, making it easier for consumers to identify and remember the product.”]
[claim claim=”Inner coatings on aluminum bottles affect branding aesthetics.” istrue=”true” explanation=”Applying inner coatings not only protects contents but also enhances the visual appeal, creating a cohesive branding experience for consumers.”]
What types of inner coatings are available for aluminum bottles?
Did you ever think about what goes into creating your favorite aluminum bottle to keep it safe and effective? Let’s explore the world of inner coatings. These coatings shape the quality of what we drink, use or apply. Coatings are very important.
Aluminum bottles have different inner coatings. Coatings include epoxy, polyester, vinyl and silicone. Each type offers unique benefits for specific uses. These features impact safety. Durability is also affected.
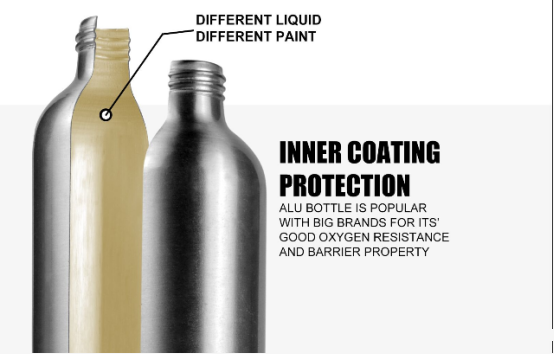
Understanding Inner Coatings for Aluminum Bottles
Aluminum bottles are increasingly favored for their lightweight, durable, and recyclable properties. However, the type of inner coating used plays a crucial role in the overall performance and safety of these containers.
Types of Inner Coatings
There are several types of inner coatings available, each serving specific purposes:
-
Epoxy Coatings
- Description: Epoxy coatings work as a barrier against moisture and oxygen. They are perfect for food and drinks. They stop contamination.
- Pros: Their durability and chemical resistance impressed me. They prevent leakage, an important factor for my products.
- Cons: However, they might not suit all contents, as they could leak chemicals. This is something to consider when choosing packaging.
-
Polyester Coatings
- Description: These coatings are great for personal care products. They are flexible and resist UV rays, so they are ideal for cosmetics.
- Pros: I like their smooth finish and color options for branding.
- Cons: They don’t block oxygen as well as epoxy. This is a trade-off that needs careful thought.
-
Vinyl Coatings
- Description: Vinyl coatings are interesting for non-food uses. They stick well and are flexible, perfect for industrial purposes.
- Pros: They’re affordable and easy to apply, good for low budgets.
- Cons: They’re not safe for high temperatures or food, which limited their use for my products.
-
Silicone Coatings
- Description: Silicone offers a non-stick surface, ideal for easy dispensing products. Very useful in spray bottles.
- Pros: They resist high temperatures and chemicals well but cost more than other options.
Coating Type | Best Suited For | Pros | Cons |
---|---|---|---|
Epoxy | Food & Beverage | Durable, chemical-resistant | Potential leaching |
Polyester | Personal Care & Cosmetics | Flexible, UV-resistant | Poor oxygen barrier |
Vinyl | Industrial Applications | Cost-effective, easy application | Limited heat resistance |
Silicone | Dispensing Products | Non-stick, high temp resistant | Higher cost |
Importance of Selecting the Right Coating
Choosing the right inner coating is vital for maintaining product quality and safety. For example, if my detergent touches a wrong coating, it might spoil or get contaminated over time. This fact has influenced how I make packaging choices with suppliers.
To learn more about choosing the right inner coatings for your aluminum bottles, check out our guide on inner coatings for aluminum2. Knowing these details can really prevent many problems later!
[claim claim=”Epoxy coatings are suitable for food and beverage applications.” istrue=”true” explanation=”Epoxy coatings provide excellent barrier properties and prevent contamination, making them ideal for food and beverage storage.”]
[claim claim=”Vinyl coatings are recommended for high-temperature applications.” istrue=”false” explanation=”Vinyl coatings are not suitable for high temperatures, limiting their use in certain applications.”]
What sealing methods can I trust to prevent leaks in my aluminum packaging?
Let’s explore sealing methods for aluminum packaging. Keeping your product secure from leaks is really important. Quality matters. Customers want satisfaction.
To stop leaks in aluminum packaging, use heat sealing, induction sealing, pressure sealing or adhesive sealing. Every method offers unique benefits. These methods suit different products and work in various conditions. Your products will stay safe and satisfy customers.
Understanding the Importance of Sealing in Aluminum Packaging
Sealing is a crucial aspect of aluminum packaging, especially for liquid products such as laundry detergents. Effective sealing methods not only prevent leaks but also maintain the integrity and quality of the product inside.
For manufacturers who prioritize product quality and environmental sustainability, understanding various sealing methods is essential.
Common Sealing Methods
Several sealing techniques are employed in aluminum packaging, each with its pros and cons:
Sealing Method | Description | Advantages | Disadvantages |
---|---|---|---|
Heat Sealing | Utilizes heat to bond materials | Strong seal, suitable for high-volume production | Requires precise temperature control |
Induction Sealing | Uses electromagnetic induction to seal | Excellent barrier against moisture and tampering | Equipment cost can be high |
Pressure Sealing | Applies pressure to create a seal | Fast process, low-cost setup | May not be suitable for all materials |
Adhesive Sealing | Uses adhesives to bond packaging | Versatile and effective for various shapes | Potential for chemical leaching |
Each of these methods has unique applications depending on the type of product and packaging requirements. For instance, heat sealing is commonly used in bulk packaging, while induction sealing is favored for its tamper-evident properties.
Factors Influencing Sealing Effectiveness
When choosing a sealing method, several factors must be considered:
- Product Type: Liquids with varying viscosity may require different sealing techniques to ensure a leak-proof seal.
- Environmental Conditions: Temperature and humidity can impact the performance of seals.
- Packaging Design: The shape and design of the aluminum container can influence the sealing method used.
Additional Considerations for Sustainable Packaging
As an environmentally conscious manufacturer, it is important to consider eco-friendly sealing options that minimize waste and use non-toxic materials.
For more insights on sustainable practices in aluminum packaging, check out eco-friendly packaging solutions3.
Conclusion: Key Takeaways (No conclusion needed here)
Understanding these sealing methods allows manufacturers to select the best approach for their specific products. By employing effective sealing techniques, companies can ensure high-quality packaging that meets customer expectations while reducing the risk of leaks.
[claim claim=”Heat sealing provides a strong seal for aluminum packaging.” istrue=”true” explanation=”Heat sealing is effective for creating durable seals in aluminum packaging, especially for high-volume production, ensuring product integrity.”]
[claim claim=”Induction sealing is the cheapest sealing method available.” istrue=”false” explanation=”Induction sealing offers excellent moisture barriers but can be costly due to the required equipment, making it less economical than other methods.”]
Conclusion
Discover the advantages of 16 oz aluminum bottles: durability, sustainability, customizable designs, effective sealing methods, and diverse applications in personal care, beverages, and pharmaceuticals.
CPI is a professional supplier of aluminum bottle packaging in China over 10 years, if you are looking for 16 oz aluminum bottle, please contact us freely, let’s help you now.
-
Explore the advantages of aluminum packaging for sustainability and product protection. ↩
-
Explore various inner coating options to ensure optimal performance and safety for your products. ↩
-
Discover detailed insights on effective sealing methods that ensure leak-proof aluminum packaging, crucial for maintaining product quality. ↩